Everything You Must Know About Alumina Ceramics
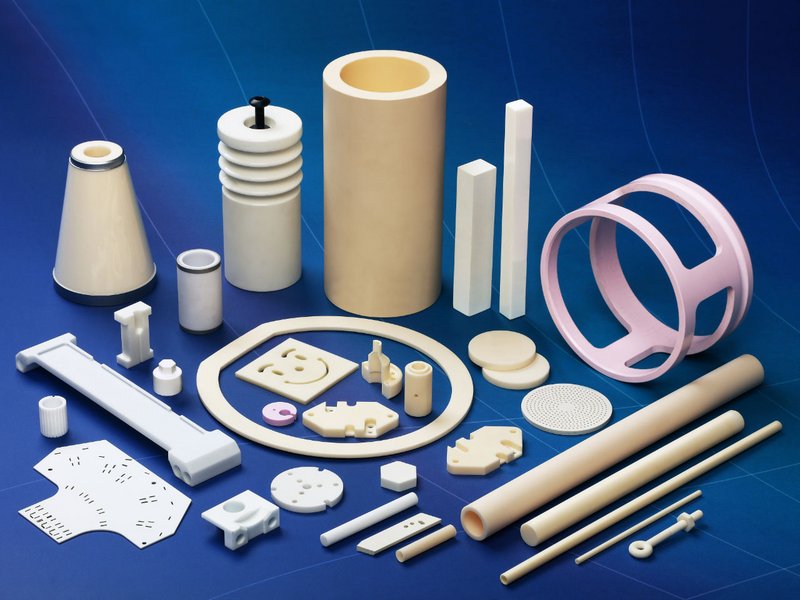
You're here to know the meaning of alumina. Alumina is a type of ceramic material with numerous benefits. It has low electrical conductivity, chemical resistance, high strength, and the ability to withstand. The material has a high melting point, and has an 9 Mohs hardness rating.
High-purity
High Purity Alumina Ceramics for Semiconductor Market Research Report contains market size segmentation, growth, and company profiles. It also provides the most important market drivers and the challenges. The report is focused on the worldwide market for alumina oxide. The report employs a five-force analysis in order to assess the market and pinpoint potential opportunities.
High-purity alumina is abrasive and versatile technical ceramic materials. They have excellent thermal and electrical insulation properties. They can be customized to fit specific needs.
Small grain size
Alumina ceramic grains are coarsened by heat treatments. These heat treatments are usually carried out at temperatures ranging from 1350 and 1400 degrees C. A large increase in grain size can reduce Vicker's hardness by around 10%. The grain size also affects the efficiency of sawing. So, the smaller the grain size, the greater the efficiency of cutting.
In light-transmitting devices such as high-pressure sodium va lamps, arc tubes and other light-transmitting devices Aluminas with coarse grain can be employed. Prothetic ceramics need to resist corrosion even at higher temperatures and are transparent, but they also must be able to maintain their strength.
Resistance to corrosion
There are a variety of ways to assess the resistance of Alumina Ceramics to corrosion. For instance, the material's chemical stability is determined by studying its resistance to alkalis and acids. The more pure the material, the better the resistance to these substances. Another method of determining the corrosion resistance of alumina is to test the material in water-based solutions that contain a high concentration of sulfuric acid.
Alumina ceramics are classified based on their Al2O3 content. The higher the percentage of ceramic seals, the higher wear and corrosion resistance. Alumina ceramics are typically composed of white, granular substance that is dense and silky. There are two kinds of Alumina two types: tabular and hydrated.
Machining
Alumina Ceramics can be machined to produce high-quality parts with precise tolerances. They also stand up to heat, chemical, as well as mechanical wear. These materials are excellent for aerospace, medical academic, and other industries. Other applications for these materials include bushings and components which are very extremely high in corrosion and electrical resistance.
Alumina is available in a range of purity levels. The typical range is 90 to 99.9% and includes Precision Ceramics working primarily with 99.7% alumina. Ceramics that are extruded easily and moldable. But, custom ceramics requires advanced diamond grinding techniques. The most advanced machining techniques have been developed to make this material more easy to machine.
Applications
Alumina Ceramics have a broad range of applications in various fields. For instance, in the medical field, they are utilized as a bone tissue substitute in orthopedic surgeries, as artificial joints, bones as well as false teeth made of porcelain. Alumina ceramics are a popular option due to their extraordinary properties and ability to withstand extreme temperatures.
Alumina ceramics can be made in a variety of methods, from granulated powder to fully fused ceramics. Sintering is the process of forming a suspension and heating of alumina in liquid. The alumina powder is usually mixed with other materials prior to being molded. This will determine the grade of the ceramic.